Schuhe aus dem 3D-Drucker
Lewis Hamilton trägt sie, Justin Bieber auch, der Branchenriese Nike arbeitet mit dem Start-up zusammen: Innerhalb weniger Jahre hat sich Zellerfeld R&D aus Stellingen zum international führenden Anbieter im digitalen Schuhdruck entwickelt. Ein von der IFB Hamburg unterstütztes Forschungsprojekt half dabei, den Produktionsprozess weiterzuentwickeln und wirtschaftlicher zu gestalten.
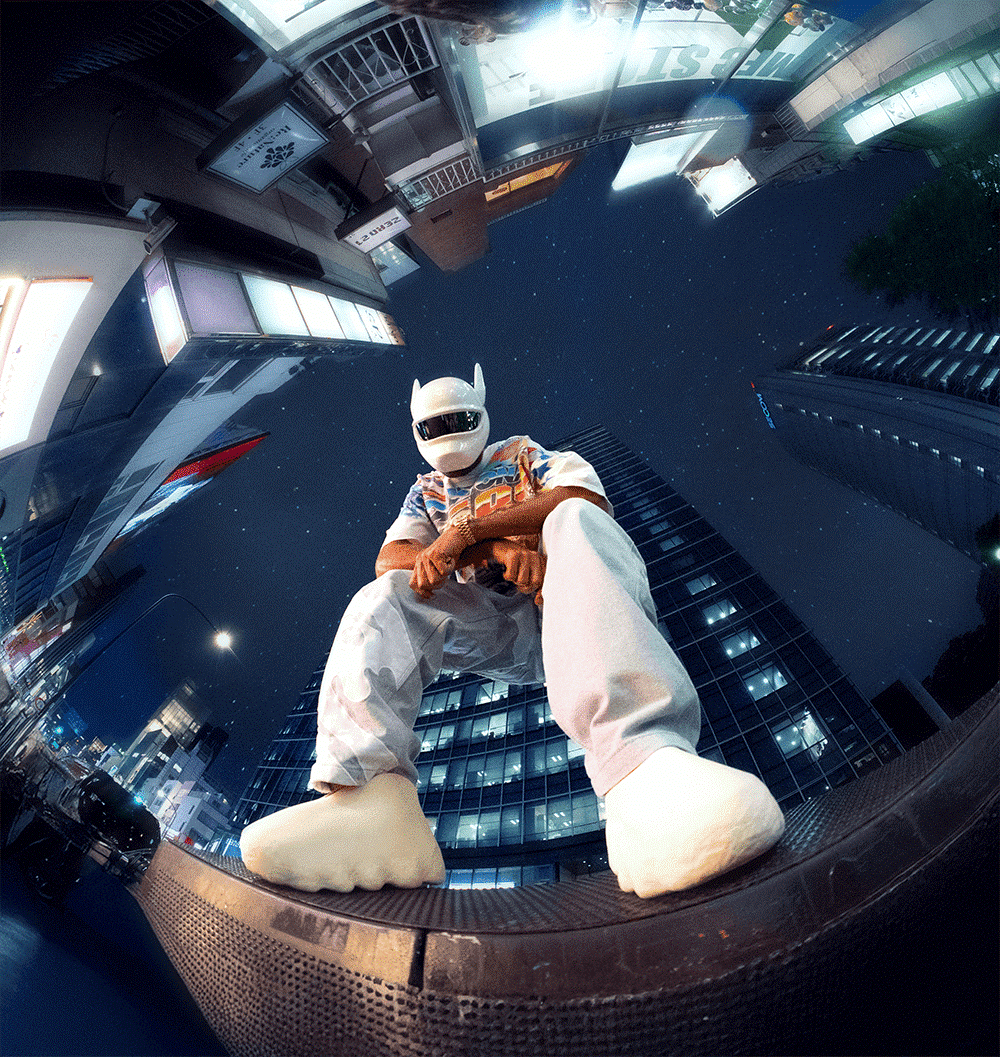
Lennard Stoever, Co-Gründer, ist gerade zurück aus Austin, Texas. Zellerfeld will dort eine Fabrik errichten. Mindestens die Hälfte der 2.000 Drucker, die das Unternehmen kürzlich bestellt hat, soll dort Schuhe produzieren, die andere Hälfte in Hamburg, wo derzeit 200 Drucker stehen. „Unsere Vision ist, auf jedem Kontinent Drucker zu haben“, sagt Stoever. „Transporte werden dann überflüssig, wir können in dem jeweiligen Land eine Kreislaufwirtschaft aufbauen. Unsere Schuhe sind ja komplett recycelbar.“
Das 2019 gegründete Unternehmen hat sehr erfolgreich eine Nische besetzt. Wasserdicht, atmungsaktiv, maßgeschneidert, frei von Schnürsenkeln und von oftmals eigenwilliger Form sind die Schuhe, die erst gedruckt werden, nachdem die Kundinnen und Kunden per Handy ihre Füße gescannt haben.
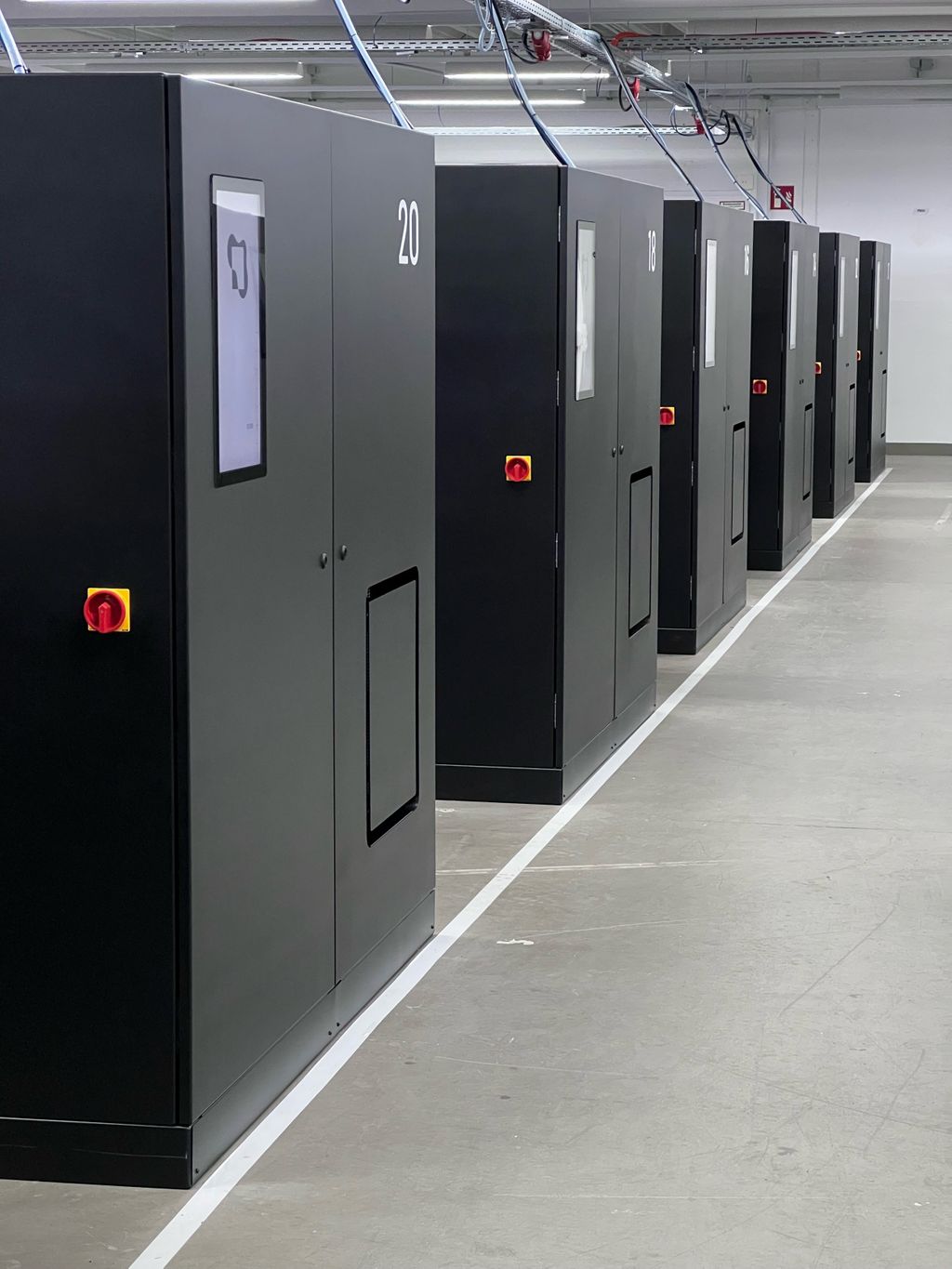
„Anders als die traditionelle Schuhindustrie mit ihrer standardisierten Massenware produzieren wir nachhaltig und individuell. Wir verstehen uns als Plattform für Creator mit Designfreiheit, jeder kann bei uns seine Schuhe kreieren. Und die sehen oft komplett anders aus als man das so kennt“, erzählt Stoever. Derzeit kosten die individuell gefertigten Schuhe rund 200 US-Dollar pro Paar – ein vergleichsweise günstiger Preis für maßgeschneiderte Produkte. Die Preisgestaltung übernehmen die Designer selbst. Langfristig sollen die Schuhe noch erschwinglicher und für ein breiteres Publikum zugänglich werden.
Die ersten Drucker hat Cornelius Schmitt, Co-Gründer von Zellerfeld R&D, in seinem Keller hergestellt. Schicht für Schicht, beginnend mit der Ferse, wird der Schuh in einem Stück mit einem flexiblen Kunststoff gedruckt. Abhängig von der Größe erfordert das bis zu 5.000 Schichtlinien und dauerte anfänglich mehr als 100 Stunden. „Inzwischen sind wir auf 36 Stunden runter und bald auf unter 24“, sagt Stoever. Eine Herausforderung des Verfahrens waren Fehler, die beim Druck passierten, und zu einem Ausschuss von rund 25 Prozent führten.
„Unser Ziel ist es, diese Fehler noch während des Druckprozesses zu erkennen und im besten Fall zu korrigieren, ohne den Druck abbrechen zu müssen“, erzählt Stoever. Für das Forschungsprojekt tat sich Zellerfeld mit dem Fraunhofer Institut für Additive Produktionstechnologien (IAPT) zusammen. Während die Wissenschaftlerinnen und Wissenschaftler vor allen die Sensorik verbesserten, optimierten die Expertinnen und Experten von Zellerfeld das maschinelle Lernen. „Das Projekt war sehr erfolgreich. Die Fehlerquote konnte bereits jetzt gesenkt werden“, meint Stoever.

Mit knapp einer Million Euro förderte die IFB Hamburg im Rahmen von PROFI Transfer das Vorhaben. Das Programm unterstützt Unternehmen aller Branchen und Größen, die in Kooperation mit Hamburger Hochschulen oder Forschungseinrichtungen innovative Projekte umsetzten wollen. Die Zuschüsse betragen bis zu einer Million Euro, die Förderquote bei Zellerfeld betrug 45 Prozent, beim Fraunhofer IAPT 100 Prozent. „Ohne die Förderung hätten wir das Projekt damals auf keinen Fall angefangen“, sagt Stoever.
Für Nike druckt das Startup den Air Max 1000, eine Weiterentwicklung des Air Max 1. Auch im High-Fashion-Bereich ist Zellerfeld angekommen, Sänger Justin Bieber und Formel 1-Fahrer Lewis Hamilton tragen die Schuhe aus dem Drucker. Bis zu 40.000 Paar kann Zellerfeld mit seinen 50 Mitarbeitenden in Hamburg derzeit herstellen, in zwei bis drei Jahren sollen es eine Million sein.