Nachhaltige Fassadendämmung per 3D-Druck
Vollständig recycelbar, CO₂-neutral in der Herstellung, kostengünstiger: Der Ingenieursdienstleister TECCON Consulting & Engineering und die Technische Universität Hamburg (TUHH) wollen traditionelle Dämmmaterialien wie Hanf oder Stroh für Gebäudefassaden mit modernen 3D-Verfahren zusammenbringen. Die IFB Hamburg unterstützt die Durchführbarkeitsstudie mit ihrem Programm PROFI Umwelt.
Der Ausgangspunkt war der Hauskauf einer Mitarbeiterin, die ihre Fassade energetisch modernisieren wollte. „Damals“, erzählt Oliver Grunewald, Architekt bei TECCON, „haben wir erstmals die Frage diskutiert: Kann man die Dämmung nicht vereinfachen? Sie effizienter und ökologischer gestalten? Durch die Anwendung neuer, innovativer Verfahren?“ Für eine Durchführbarkeitsstudie tat sich der Ingenieursdienstleister mit der TUHH zusammen, mit dem Institut für Industrialisierung Smarter Werkstoffe (ISM). Jetzt, kurz vor Abschluss der Studie, zeichnet sich ab: Das Verfahren funktioniert, aber trivial ist es nicht.
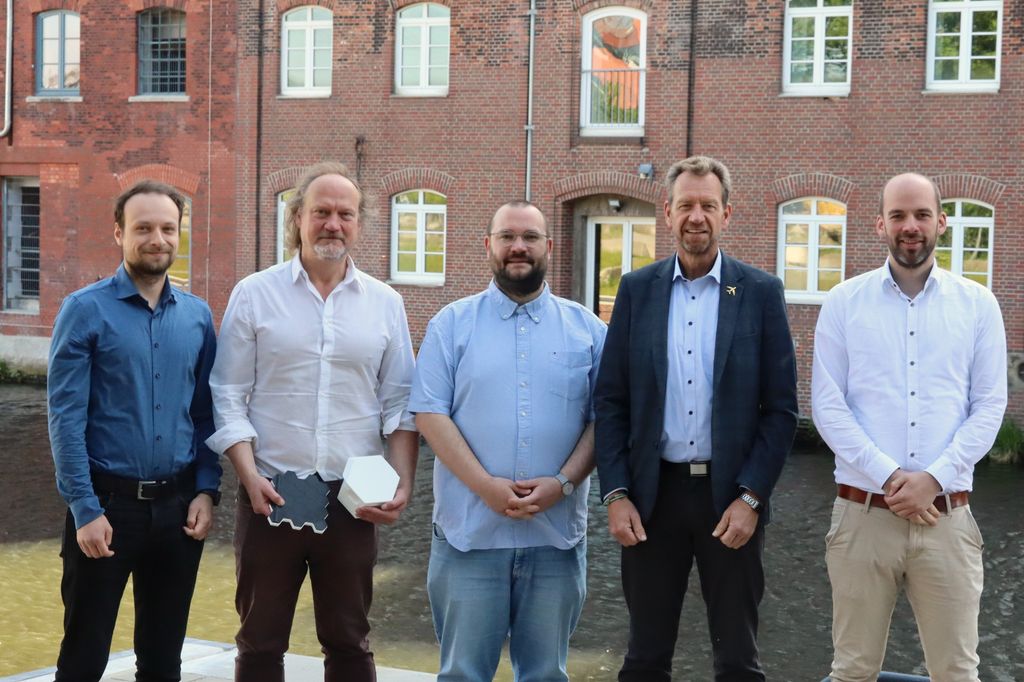
Für Metalle oder Kunststoff ist der 3D-Druck längst etabliert, nicht aber für natürliche Materialien. „Das kommt gerade auf“, sagt Maximilian Keller, Projektingenieur am Institut für Materialprüfung an der TUHH. Beispielsweise lassen sich Holz- oder Hanffasern in Form einer Paste auch verdrucken. „Wir haben inzwischen Materialien und Strukturen identifiziert, die sich für die Dämmung eignen“, berichtet Keller. „Das Potenzial ist vorhanden, aber der Weg ist nicht einfach.“ Die Herausforderungen sind nicht nur technischer Natur, das Material muss, bevor es zugelassen wird, im Zuge einer Zertifizierung auch zahlreichen Anforderungen genügen wie etwa dem Brandschutz.
Echte Pionierarbeit also. Vor Ort auf der Baustelle sollen die Dämmplatten eines Tages gedruckt werden, so die Vision der Macher, individuell angepasst an die Fassaden. Kreislauffähig, also am Ende des Lebenszyklus vollständig recycelbar, soll das Material sein und gegenüber der herkömmlichen EPS-Fassadendämmung bis zu 90 Prozent CO₂ einsparen. Auch von deutlichen Kosteneinsparungen gehen die Ingenieure aus.
Mit insgesamt 128.000 Euro unterstützt die IFB Hamburg die Machbarkeitsstudie in Rahmen des Förderaufrufs Green Potential Screening in ihrem Programm PROFI Umwelt (Transfer). Das fördert die Entwicklung innovativer, marktfähiger Produkte, Verfahren oder Dienstleistungen, die einen Beitrag zum Klima- und Umweltschutz leisten mit Zuschüssen bis zu 500.000 Euro bei Einzelprojekten und bis zu 1 Million Euro bei Kooperationsprojekten. Infrage für die Förderung kommen Unternehmen aus allen Branchen und Technologien sowie die mit ihnen kooperierenden Hochschulen oder Forschungseinrichtungen.
Für TECCON war es nicht das erste Projekt, das von der IFB Hamburg gefördert wurde. „Ohne diese Unterstützung könnten wir als Ingenieurbüro die Forschung gar nicht durchführen“, betont Jörg Manthey, Director Business Development. „Auch diese Studie hätten wir ohne die Förderung nicht verwirklichen können.“
Ein Nachfolgeprojekt zeichnet sich bereits ab. Wenn alles gut läuft, könnten die ersten per 3D-Druck hergestellten nachhaltigen Dämmplatten in zwei bis drei Jahren auf den Markt kommen. „Da geht die Reise hin“, ist sich Jörg Manthey sicher. Zunächst an Einfamilienhäusern oder kleinen Objekten soll die Technologie ausprobiert werden, bevor es um die Skalierbarkeit geht. Gut möglich, dass die Ingenieure von TECCON selbst zu Produzenten werden. „Vielleicht gehen wir auch eine Partnerschaft ein, das ist noch nicht entschieden“, sagt Jörg Manthey.